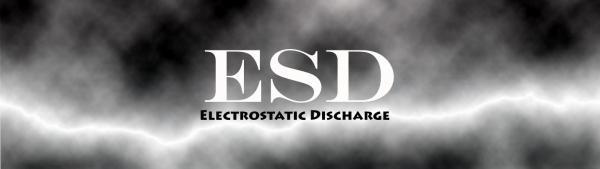
We all have experienced static electricity. It is a natural occurrence that will help in our understanding of electrostatic discharge. So, in order to have a “discharge”, one must first have a “charge”, right? This charge occurs when two different materials rub against each other – one becomes positive charged and the other negatively. The charge will remain until it is removed (discharged) by way of electric current or electrical discharge. Simply put, electrostatic discharge (ESD) is the release of static electricity.
This daily phenomenon called electrostatic discharge can be problematic for manufacturers of sensitive electronic components. Particularly when it only takes about 25 volts to irreparably damage a circuit board assembly. This can easily and innocently happen without anyone realizing. As such, an effective policy on managing ESD in an electronics manufacturing workplace is vital to quality control.
To complicate matters even more, most materials can be sources for electrostatic build-up. Our skin, clothes, glass, nylon, fabric, metals and many more materials can develop a charge. Each with varying storage capacities that correlate to the amount of electrostatic charge accumulation – thus a recipe for disaster in a manufacturing setting and handling sensitive electronic components. A damaged board that fails in the field can be catastrophic and result in significant loss. For this reason, most manufacturers have a defined written and practiced ESD policy.
Controlling and Managing ESD
We must first understand which material combinations cause more static electricity than others. Some materials give up electrons when in contact with certain materials and will have a positive charge. While others attract electrons when brought into contact with certain materials and become negative in charge. The imbalance of electrons on a surface is what results in electrostatic discharge. A quick audit of the area where sensitive electronic parts will be handled and stored may help identify the high-risk electrostatic materials that should be avoided. The triboelectric effect, though known to be unpredictable, will help generalize which materials through friction become electrically charged.
Your best defense against electrostatic damage is to have a well written and practiced ESD policy. When developing such a plan, compliance verification requirements for wrist straps, footwear, flooring materials, work surfaces, wrist strap connection points, shielding bags, clothing and best practices should be outlined. It’s important to identify areas that need ESD protection. It is surprising how many different areas this can entail. Once determined, clearly mark these areas commonly referred as electrostatic protected areas (EPAs). Visibility is key and serves as a constant reminder to everyone when entering these areas. Typical EPA areas will include:
- Shipping, Receiving, & Packaging
- Storage Areas and Warehouses
- Inspection
- Assembly
- Testing
- R&D
- Field Service Repair
- Cleanrooms
- Laboratories
ESD Policies usually entail an initial training component with periodic refreshers. A person within the organization should be appointed to lead the “charge” (ha, pun intended), develop the ESD policy, organize necessary training and assure compliance. Accompanying an ESD policy is usually a procedure manual to which staff can be referred.
In order to manage and control electrostatic discharge, an entire ESD market of products has been created. Companies can purchase clothing, footwear, bags, coffee mugs, garbage cans, labels, floor mats, and testers to eliminate electrostatic discharge. Common products used in electrostatic areas include the following:
- ESD Wrist Strap – is a conductive bracelet that is used to safely ground a person working on electronic equipment. These bracelets help to prevent the buildup of static electricity on their body which can result in electrostatic discharge.
- ESD Foot Strap – is a device that is worn on a person’s foot that when properly worn and used on ESD flooring will help prevent the buildup of static electricity on a person’s body.
- ESD Smock – is an ESD garment laced with conductive threads to help prevent normal clothing from coming into contact with ESD sensitive devices. It creates a wearable version of a faraday cage.
- Antistatic Bag – is a used for storing or shipping electronic components and assemblies.
- ESD Test Meter – is equipment used to help locate sources of ESD and to help check the performance of wrist straps, foot grounders, ESD shoes and other antistatic products.
- Ionizing Fan – is a special fan that neutralizes/eliminates static electricity from an area or surface.
In summary, electrostatic discharge can be very costly to companies. Managing electrostatic discharge is critical for electronics manufacturers and entails an ESD policy and procedures. Understanding the causes of electrostatic charges and discharges and means to protect products from ESD play a key role in developing such policies. An effective ESD program requires solid training where everyone understands the “who”, “what”, “where”, “when”, and “why’s” of controlling ESD in the workplace.